Infill 3D Printing
What is Infill 3D printing?
3D printing has two zones, the shell and the fill. The shell refers to the outer walls of the model, whereas the fill or infill 3D printing refers to the amount of material inside the piece printed. A higher infill provides more strength, but at the cost of a higher print time, weight and amount of material used. Very rarely does a 3d printed model have 0% or 100% infill, a percentage in between determines how much material would be required to print, the time to print, the strength, buoyancy and the weight of the final product. Different patterns of infill grant it different perks which will be discussed below.
Infill 3D printing pattern types
Line
The lines infill pattern contains lines printed in one direction (either along with the X or Y-axis) in every other layer.
Honeycomb
This infill 3D printing pattern is in the shape of a honeycomb. This pattern has moderate strength and print time.
Grid
This is similar to the line infill 3D printing pattern. The difference is that it contains two-dimensional lines printed on every layer, with twice as much space between the lines.
Triangle
This infill 3D printing pattern has triangular shapes created by intersecting lines
Tri-hexagon
This contains an assortment of lines going in three directions in the XY-plane, creating hexagonal patterns with triangles in between.
Cubic
This pattern produces stacked cubes that are at a 45-degree angle to both the X and the Y-axis.
Octet
This infill 3D printing pattern is similar to the cubic pattern but differs in the fact that the cubes are not sloped with respect to the X and Y-axis.
Gyroid
These would be the most unique patterns among all others with a wavelike shape. The pattern is aesthetically pleasing and is isotropic.
Concentric
This infill 3D printing pattern is composed of concentric lines matching the part’s perimeter shape. It is quick to print and consumes a lot less material than a lot of other infill patterns.
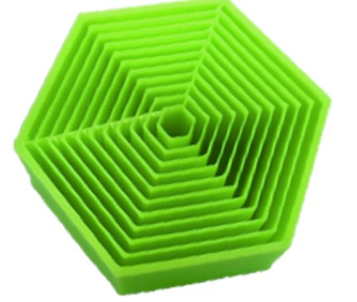
Which infill 3D printing pattern should I use?
Factors like flexibility, strength, print time and the amount of material used to have to be looked at before choosing an infill pattern.
Lines: Quick 2D infill, for models that do not require much strength and have to print quickly. Uses less material and the print turns out light
Grid: Strong 2D infill, for everyday prints. Takes a moderate amount of time and material to complete with respect to other patterns.
Triangles: Strong 2D infill 3D printing, similar in strength to the grid and tri-hexagon patterns.
Tri-hexagon: Strong 2D infill, similar in strength to grid and triangle patterns.
Cubic: Strong 3D infill but takes longer time and more material than other infill patterns
Octet: Strong 3D infill
Gyroid infill: Infill with increased strength for the lowest weight.
Concentric: Provides flexibility and is economical
Infill 3D printing density
Infill density refers to the amount of printing material filled inside the walls of the model. A higher infill density will create a more solid object resulting in higher strength. For non-functional parts, prototypes or models, an infill percentage of around 15% is enough, for parts that withstand a moderate load, an infill percentage of around 20% is sufficient and for parts that take on a higher load, an infill of 60% should be taken. A percentage greater than 60 has diminishing returns on strength and is usually not required.
Importance of Infill 3D printing
Infill is required for the whole volume of the model. That means that slight variations in the percentage or type of infill of higher volume parts can vary the cost and characteristics of the model enormously. It is important to choose the correct infill type for the most effective and economical way to make your model. A higher infill percentage will result in a longer print time, especially on models with a large interior volume. Many printers allow for variable infill density settings on progressive printed layers. For example, if you want a part’s base to have a 20% infill up until layer 20 and then switch to a 40% infill, variable settings allow you to do this. Hence, well-engineered models can be both very strong and very economical to print.
Conclusion
Infill density and pattern can impact a lot of important characteristics of the model to be printed, hence it is crucial to understand the use case and print accordingly. It is to be noted that infill is only one of the many important factors that determine the strength of the print. The thickness of the outer shell and the orientation of the part are also factors that have to be given proper consideration.
Get your First 3D Print for FREE – Click Here